EN ISO 11612:2015
Protective clothing - Clothing to protect against heat and flame - Minimum performance requirements
This International Standard specifies performance requirements for protective clothing made from flexible materials, which are designed to protect the wearer’s body, except the hands, from heat and/or flame. For protection of the wearer’s head and feet, the only items of protective clothing falling within the scope of this International Standard are gaiters, hoods, and overboots. However, concerning hoods requirements for visors and respiratory equipment are not given.
The performance requirements set out in this International Standard are applicable to protective clothing which could be worn for a wide range of end uses, where there is a need for clothing with limited flame spread properties and where the user can be exposed to radiant or convective or contact heat or to molten metal splashes.
This International Standard is not applicable to protective clothing that is specified by other International Standards.
General requirements
- Pocket liner must also meet flame spread and heat resistance
- Hardware penetrating the outer material of a heat and flame protective garment shall not be exposed to the innermost surface of the garment.
Additional design requirements for letter code D and E
- The sleeves of jackets and coveralls and the lower leg regions of trousers, coveralls and bib + brace shall not have turn-ups.
- External pockets on jackets, trousers, coveralls and bib + brace, other than side pockets below the waist which do not extend more than 10° forward of the side seam, shall be covered by flaps at least 20 mm wider than the opening of the pocket in order to prevent the flap from being tucked into the pocket.
- Patch pockets shall be made from materials meeting the same protection indices and the same levels for these indices as the rest of the garment.
- Overlapping seams on the outside of the garment shall be downward facing and secured in this position.
- Closures shall be designed with a protective cover flap on the outside of the garment. The maximum distance between buttonholes shall be 150 mm. If zippers are used, the slide fastener shall be designed to lock when completely closed. Cuffs may be provided with closures to reduce their width. The closure and any fold which it creates shall be on the underside of the cuff. Neck openings shall be provided with closures. Trousers may have side slits which shall have a means of closure and the slit and closure shall be covered.
Hardware and accessories demands
- Hardware [e.g. touch and close (hook and pile) fasteners, etc.], whether it is exposed or covered when all closure systems in the garment are in the closed position, shall be tested separately by applying the test flame to the outer surface of the component assembly containing hardware exactly as designed in the garment. The hardware shall remain functional after the test.
- Labels, badges, retro-reflective materials, etc., which are applied to the outermost surface of the garment, shall be tested in combination with the outer layer to make it possible to take samples with the dimensions as indicated in ISO 15025. They shall be tested by applying the flame to the outer surface of the items. They shall have the same flammability behavior as the outer layer of the garment.
Seam demands
- For seams, three specimens containing a structural seam shall be tested in accordance with ISO 15025:2000, Procedure A. Specimens shall be oriented with the seam running up the centreline of the test specimen so that the burner flame impinges directly upon it. The seams shall remain intact.
- If the garment is multilayer, specimens of the component assembly including seams shall be tested both by applying the flame to the surface of the outer material of the garment and to the innermost lining of the garment and shall meet the requirements, including that no specimen shall suffer hole formation except for an interlining that is used for specific protection other than heat protection, for example, liquid penetration.
- For seams, three hemmed specimens containing a structural seam shall be tested in accordance with ISO 15025:2000, Procedure B. Specimens shall be oriented with the seam running up the centreline of the test specimen so that the burner flame impinges directly upon it. The seams shall remain intact.
- If the garment is multilayer, hemmed specimens of the component assembly including seams shall be tested in accordance with ISO 15025:2000, Procedure B, by applying the flame to the edge of the multilayer assembly and shall meet the requirements.
- Seam strength, in accordance with ISO 13935-2, of the outer material or outer garment material of the clothing assembly shall give a breaking load of at least 225 N for woven textiles
Manikin testing for prediction of burn injury
This optional test in accordance with ISO 13506 and is performed on each ROOTS garment, carried out by the British Textiles Technology Group (BTTG) or AITEX after a specified number of washing/drying cycles on a RALPH (Research Aim Longer Protection against Heat) manikin. This test can be carried out at 3 seconds, but at ROOTS we go beyond and test our garments at 4 seconds which is also advised in the standard EN ISO 11612. It may not seem to be a huge difference, just one second but one extra second generates a third more energy (84 kJ per mtr2 per second). During testing, temperatures are reached between 800- 1.000˚C. Reports and prediction on injury by burns as videos are available from every single test. Throughout the manikin test, we are also able to prove that the use of the logo’s (heat seal transfers, embroidered badges, etc.), do not have a negative effect on the flame spread.
BURN INJURY PREDICTIONS
Although the relatively ‘new’ EN standard EN ISO 11612 (protective clothing – clothing to protect against heat and flame) is already a huge improvement as compared to the ‘old’ and less demanding EN531 it is still possible for garment makers to present products to the market place that are potentially unsafe.
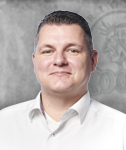
Questions?
Get in contact with our QHSE + CSR Manager,
Marco Kremers, he'd love to help you.
Call: +31 (0)10 2955 955